Raport zza zamkniętych drzwi - Szafrański w fabryce butów.
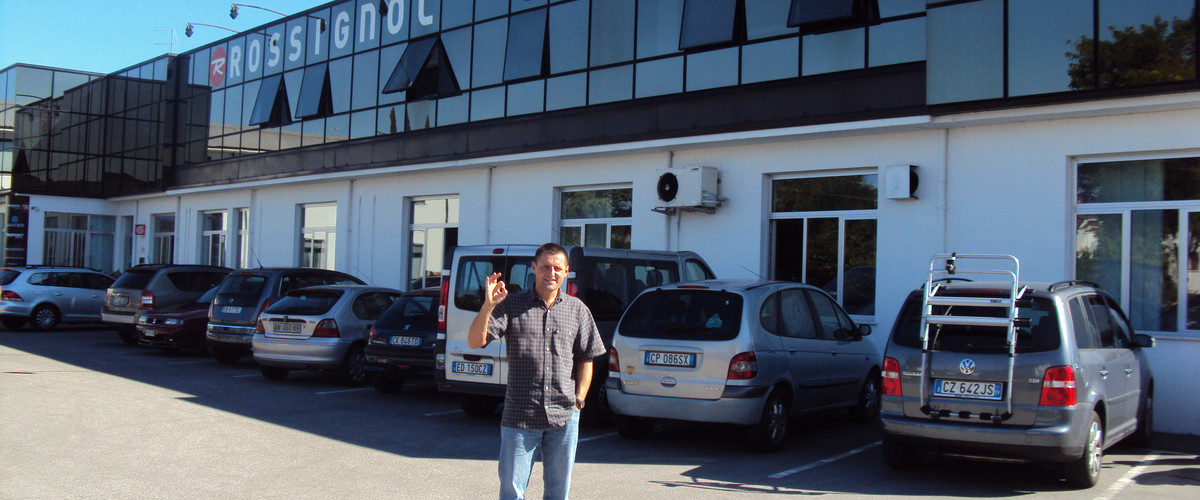
Montebelluna to mała, bardzo spokojna mieścina leżąca w północnej części Włoch. Podobnych miasteczek jest tysiące, ale to właśnie Montebelluna było celem mojej wycieczki. Jej powód był jeden: fakt, że projektuje i produkuje się w niej prawie wszystkie najlepsze buty narciarskie na świecie.
Dla każdej osoby interesującej się sportami zimowymi jest to miejsce niezwykłe i ważne. Mieszczą się tu fabryki takich producentów, jak Lange, Nordica, Atomic, Head, Salomon oraz wielu innych. Co ciekawe nie brakuje tu również firm związanych z innymi dziedzinami np.: Geox’a, czy Sidi, które produkują znakomite buty rowerowe i motocrossowe.
Otworzyć zamknięte drzwi
Dzięki zaproszeniu Lange udało mi się przekroczyć strzeżone drzwi i zobaczyć na własne oczy, jak się to wszystko odbywa w praktyce. Dla mnie, zgłębiającego zagadnienie butów narciarskich, było to doświadczenie bezcenne. Już po kilku spojrzeniach pojawiła się pierwsza refleksja: takie buty nie mogą być tanie. Cały proces produkcji jest naprawdę złożony. Przy tworzeniu butów Lange pracuje 77 osób, z czego 54(!) w biurach. Zwróćcie uwagę na proporcje zatrudnienia biuro – hala produkcyjna. Naprawdę dużo testują, kombinują i wymyślają, aby doprowadzić do produkcji pierwszych prototypów.
Wirtualne symulacje
Muszę przyznać, że na początku zwiedzania spotkało mnie małe rozczarowanie: całkowity zakaz fotografowania. Jakoś przełknąłem tę gorzką pigułkę i ruszyłem dalej. Wizyta zaczynała się w sporej sali open office mieszczącej kilkanaście komputerów, przy których siedzieli różnego rodzaju specjaliści odpowiedzialni za poszczególne elementy buta. Mnóstwo wirtualnych symulacji: wtrysku mieszanki, napięć, pracy klamer. Niektórym może wydawać się to nudne, innym pasjonujące.
Praca nad butami zaczyna się jednak jeszcze wcześniej. Obok pracowni z komputerami ulokowana jest mała salka do zbierania informacji. Znajduje się w niej skaner stopy 3D posiadający ogromną bazę zeskanowanych stóp, z których komputer wyciąga średnią. Tuż obok jeszcze bardziej niezwykły skaner: do prześwietlania i kopiowania dowolnych przedmiotów twardych, w tym przypadku butów narciarskich (jak łatwo się domyślić najczęściej butów konkurencji). To właśnie z tego miejsca dane przesyłane są do projektantów, którzy przygotowują wirtualny model.
Kolejny etap prac polega na wykonaniu specjalnej matrycy o odpowiednim kształcie i grubości ścianek. Taki model można już wziąć do ręki. Równolegle wykonuje się prototypy klamer i butków wewnętrznych. Wszystko z małych elementów składane ręcznie. Po przetestowaniu i zaakceptowaniu wykonuje się pierwsze prototypy poddawane wymyślnym torturom, wszystko w warunkach zbliżonych do właściwych: wilgoć i mróz (w chłodziarkach). Pamiętacie z Ikei maszynę symulującą siadanie na krześle? Tutaj podobnie – but „katowany” jest przeróżnie „katowany” i powinien wytrzymać więcej niż 100 000 ugięć. Bardzo ciekawe jest mierzenie flex-indeksu (o tym w innym artykule), efektownie wyglądają również crash-testy wykonywane w chłodni przy temperaturze -20 C.
Produkcja i mały pokoik
Druga część fabryki to produkcja. Ogromne wtryskarki pracują 24 godziny na dobę. Pod ciśnieniem plastik toczony jest w specjalne metalowe formy. Wykonanie każdej kosztuje 100 000 euro. Niesamowity majątek, biorąc pod uwagę, że każdy model i każdy rozmiar to inna forma, a jest ich naprawdę sporo. Co ważne, Lange chwali się, że odpady przerabia w 100% w obrębie samej fabryki.
Dalej pozostaje poskręcać poszczególne części i zapakować towar. Ten etap pomijam jako mało ciekawy. Na samym końcu znajduje się jeszcze jedno intrygujące pomieszczenie – mały pokoik, przez który przechodzą wszystkie sportowe buty: Race Department. Jeden Mistrz i mały warsztat. Stefano skręca buty dla każdego zawodnika indywidualnie, posługując się specjalnie wypełnioną kartą opisującą potrzeby każdego osobno: jaki dół, jaka cholewka, gdzie poszerzyć, gdzie podszlifować, jak zeszlifować, na jaki kąt. Praca trochę przypomina klocki, serwisant składa tylko około 2 pary butów dziennie.
W momencie mojej wizyty składane były buty dla JB Grange powracającego w tym sezonie. Klimatu temu pomieszczeniu dodają powieszone wszędzie plakaty z dedykacją i podziękowaniami kierowanymi do Stefano od takich sław, jak Defago czy Riesch. Jak taki proces przygotowania wygląda w praktyce, nie napiszę, niech pozostanie to tajemnicą tamtego pokoju oraz… mojego warsztatu. Mogę tylko powiedzieć, że w ciągu pół godziny nauczyłem się w tym małym pokoiku bardzo wiele.
Podsumowując: wizyta była bardzo pouczająca. Na pewno wielokrotnie będę do niej wracał we wspomnieniach. Kilka faktów, na które zwróciłem szczególną uwagę, opiszę też szerzej w następnej publikacji.